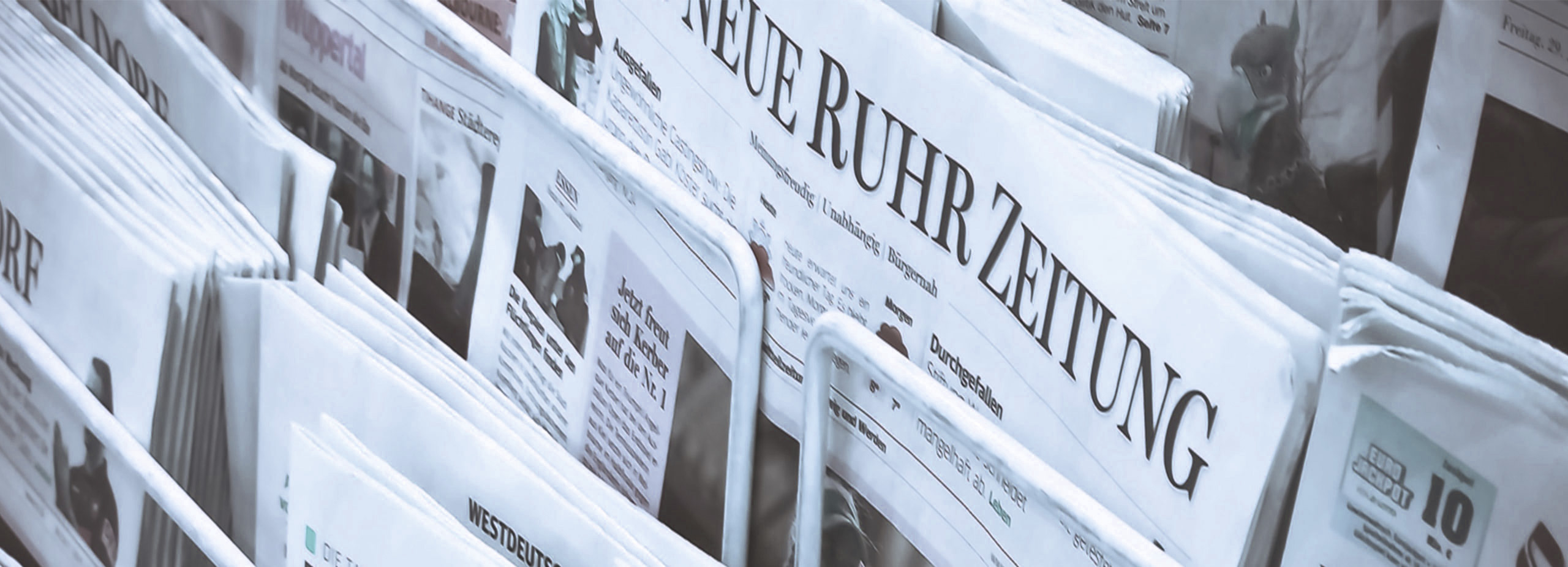
There are these tips for tool setting and debugging of lathe processing!
23.Aug 2022
Due to the frequent replacement of processed parts and the limited factory conditions, we have been programming, setting tools, debugging and completing the processing of parts by ourselves for ten years. The operation skills are summarized as follows. There are these tips for tool setting and debugging of lathe processing!Tool setting is divided into tool setting instrument and direct tool setting. Most lathes in our factory have no tool setting instrument, and they are direct tool setting. The tool setting skills mentioned below are direct tool setting.
First select the center of the right end face of the part as the tool setting point and set it as the zero point. After the machine tool returns to the zero point, each tool that needs to be used will set the tool with the center of the right end face of the part as the zero point; When the tool touches the right end face, input Z0 and click to measure, the measured value will be automatically recorded in the tool compensation value of the tool. This means that the z-axis tool is aligned, the x-axis tool is for trial cutting and tool alignment, and the outer circle of the part is less. Input X20 for the measured outer circle value (for example, X is 20mm). Click to measure, and the tool compensation value will automatically record the measured value. At this time, the x-axis is also aligned; This tool setting method will not change the tool setting value even if the machine tool is powered off and restarted. It can be applied to the production of the same part in large quantities for a long time, and there is no need to reset the tool when the lathe is closed.
After the parts are programmed and the tools are aligned, trial cutting and debugging shall be carried out. In order to prevent program errors and tool alignment errors, which may cause machine collision accidents, we should first carry out empty travel simulation processing, and translate the tool to the right in the coordinate system of the machine tool by 2-3 times of the total length of the parts; Then start the simulation processing. After the simulation processing is completed, confirm that the program and tool setting are correct, and then start the processing of the parts. After the first part is processed, conduct self inspection and confirm that it is qualified, and then find a full-time inspection and inspection. After the full-time inspection is confirmed to be qualified, it means that the debugging is completed.
In addition, it is a step-by-step process to master the operating skills of CNC machine tools, which can not be achieved overnight. We The transportation is very convenient. Since the establishment of the company, it has adhered to the business philosophy of "honest service, quality and quantity, continuous improvement and customer first" to provide customers with good delivery time and quality.