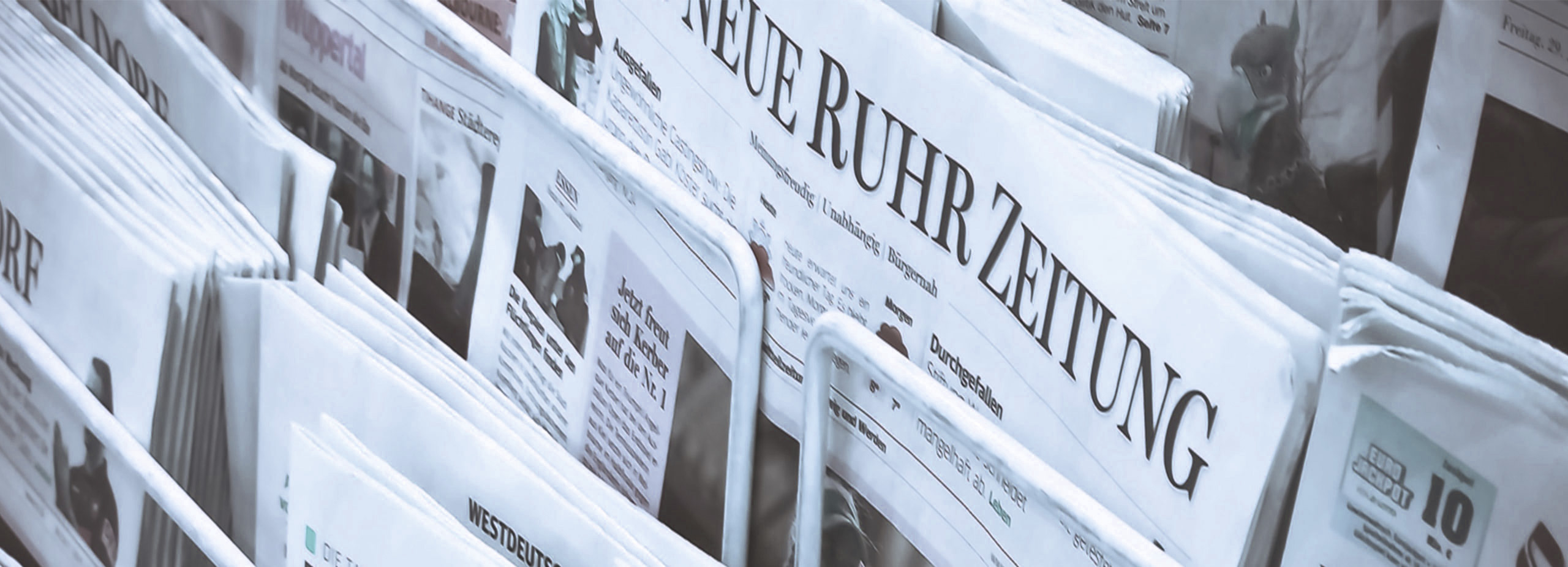
Three principles of NC machining process
23.Aug 2022
1. Principle of maximum process concentration and one-time positioningGenerally speaking, CNC machine tools, especially machining centers, allow the maximum concentration of parts processing procedures. This means that parts should be completed in a set of fixtures whenever possible. This can reduce the number of machine tools and processing time, reduce unnecessary positioning errors, and improve productivity.
In the processing of highly coaxial hole system, the processing of all coaxial hole systems must be completed through continuous tool change after one installation, and then the holes at other positions can be processed to eliminate the influence of repeated positioning errors. The coaxiality of the hole system is improved.
During NC machining, it shall be divided according to factors such as machining accuracy, rigidity and part deformation, and the machining process shall be divided according to the separation of rough machining and finish machining. This means that semi finishing and finishing are performed after all rough machining is completed. For some machined surfaces, rough machining, semi finish machining and finish machining must be carried out in this order. During rough machining, it is necessary to give full play to the performance and cutting performance of the machine tool to ensure the machining quality. Ensure the durability of the tool and the rigidity of the machine tool fixture tool workpiece process system, and use more cutting. Obtain the machining conditions of each part edge as evenly as possible before finishing. In the finishing process, the machining accuracy and surface quality of parts are mainly guaranteed. Therefore, in the finishing process, the final contour of the part must be continuously completed until the last cut. In order to ensure the machining quality, under normal conditions, the tolerance of fine machining must be between 0.2 and 0.6 mm. It is suggested to leave time between rough machining and finish machining so that the deformation of parts after rough machining can be fully recovered before finishing machining. To improve the machining accuracy of parts.
3. The principle of "near first, far later, and behind the hole first".
According to the distance between the machining parts and the tool setting point, the parts closer to the tool setting point are usually processed first, and the parts farther from the tool setting point are post processed to reduce the tool moving distance and idle time. In turning, moving closer before moving farther also helps to maintain the rigidity of the blank or semi-finished product and improve the cutting conditions. For machined parts with both milling and boring, the milling and boring sequence can be performed. Milling a flat surface will cause high cutting resistance and easily deform parts. The surface is first milled and then drilled to allow a period of recovery. After the deformation is restored, boring helps to ensure the machining accuracy of the hole. Secondly, boring before milling will cause burr and flash in the hole and affect the assembly of the hole.